Latest Thin Film Resistor Specifications
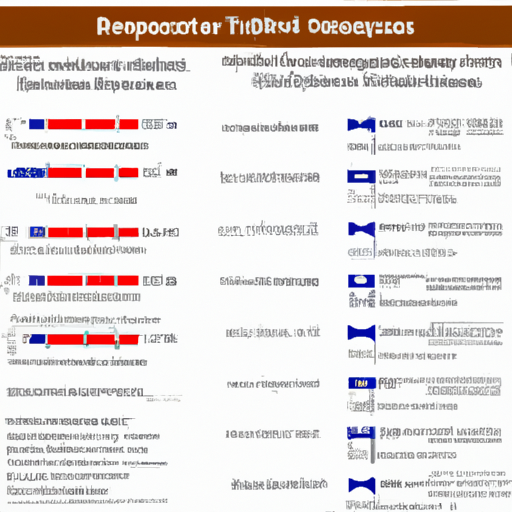
I. Introduction
A. Definition of Thin Film Resistors
Thin film resistors are electronic components that utilize a thin layer of resistive material deposited on a substrate to control the flow of electric current. Unlike traditional resistors, which are typically made from bulk materials, thin film resistors offer superior performance characteristics due to their unique construction and material properties.
B. Importance of Thin Film Resistors in Electronics
Thin film resistors play a crucial role in modern electronics, providing precise resistance values, excellent temperature stability, and low noise characteristics. They are widely used in applications ranging from consumer electronics to aerospace, where reliability and performance are paramount. As technology advances, the demand for high-performance resistors continues to grow, making thin film resistors an essential component in the design of sophisticated electronic systems.
C. Purpose of the Article
This article aims to provide an overview of the latest specifications and advancements in thin film resistors, highlighting their significance in various applications and the ongoing innovations in materials and manufacturing processes.
II. Overview of Thin Film Resistor Technology
A. Historical Background
1. Development of Thin Film Technology
The development of thin film technology began in the mid-20th century, driven by the need for smaller, more efficient electronic components. Early thin film resistors were primarily used in military and aerospace applications, where performance and reliability were critical.
2. Evolution of Materials and Manufacturing Processes
Over the years, advancements in materials science and manufacturing techniques have led to the creation of more sophisticated thin film resistors. The introduction of new materials, such as tantalum nitride and nickel-chromium, has improved the performance and reliability of these components, making them suitable for a wider range of applications.
B. Basic Principles of Operation
1. Structure and Composition
Thin film resistors consist of a thin layer of resistive material, typically ranging from a few nanometers to several micrometers in thickness, deposited on a substrate. The choice of substrate material, such as ceramic or silicon, can significantly impact the resistor's performance.
2. Mechanism of Resistance in Thin Films
The resistance in thin film resistors arises from the interaction of electrons with the resistive material. The thinness of the film allows for a more uniform distribution of current, resulting in lower noise and improved stability compared to traditional resistors.
III. Key Specifications of Thin Film Resistors
A. Resistance Values
1. Range of Resistance Values Available
Thin film resistors are available in a wide range of resistance values, typically from a few ohms to several megaohms. This versatility makes them suitable for various applications, from precision measurement devices to high-frequency circuits.
2. Tolerance Levels and Their Significance
Tolerance levels indicate the accuracy of the resistance value, with thin film resistors offering tolerances as low as ±0.01%. This high level of precision is essential in applications where even minor variations in resistance can lead to significant performance issues.
B. Temperature Coefficient of Resistance (TCR)
1. Definition and Importance
The temperature coefficient of resistance (TCR) measures how much a resistor's resistance changes with temperature. A low TCR is crucial for applications requiring stable performance across varying temperatures, such as in automotive and aerospace systems.
2. Latest Advancements in TCR Specifications
Recent advancements have led to thin film resistors with TCR values as low as ±5 ppm/°C, significantly enhancing their performance in temperature-sensitive applications.
C. Power Rating
1. Explanation of Power Handling Capabilities
Power rating refers to the maximum power a resistor can dissipate without overheating. Thin film resistors typically have power ratings ranging from a few milliwatts to several watts, depending on their size and construction.
2. Comparison with Other Resistor Types
Compared to thick film and wire-wound resistors, thin film resistors generally offer higher power ratings in smaller packages, making them ideal for compact electronic designs.
D. Voltage Rating
1. Maximum Voltage Specifications
Voltage rating indicates the maximum voltage a resistor can withstand without failure. Thin film resistors can handle voltages ranging from a few volts to several hundred volts, depending on their design and materials.
2. Impact on Circuit Design and Performance
Understanding voltage ratings is crucial for circuit designers, as exceeding these limits can lead to resistor failure and circuit malfunction. Thin film resistors' high voltage ratings make them suitable for high-performance applications.
E. Noise Characteristics
1. Types of Noise in Resistors
Resistors can generate various types of noise, including thermal noise, shot noise, and flicker noise. Thin film resistors are known for their low noise characteristics, making them ideal for sensitive applications such as audio and precision measurement.
2. Latest Specifications for Noise Performance
Recent developments have led to thin film resistors with noise levels as low as -40 dB, significantly improving the performance of circuits where noise can adversely affect signal integrity.
IV. Materials Used in Thin Film Resistors
A. Common Materials
1. Nickel-Chromium (NiCr)
Nickel-chromium is one of the most widely used materials for thin film resistors due to its excellent stability and resistance to oxidation.
2. Tantalum Nitride (TaN)
Tantalum nitride is gaining popularity for its high thermal stability and low TCR, making it suitable for high-performance applications.
3. Other Emerging Materials
Research is ongoing into alternative materials, such as graphene and carbon nanotubes, which promise even better performance characteristics.
B. Impact of Material Choice on Performance
1. Stability and Reliability
The choice of material directly impacts the stability and reliability of thin film resistors. High-quality materials ensure consistent performance over time, even in challenging environments.
2. Environmental Considerations
As environmental concerns grow, manufacturers are exploring eco-friendly materials and processes to reduce the environmental impact of thin film resistor production.
V. Manufacturing Processes
A. Deposition Techniques
1. Sputtering
Sputtering is a widely used deposition technique that involves ejecting material from a target onto a substrate, creating a thin film. This method allows for precise control over film thickness and composition.
2. Chemical Vapor Deposition (CVD)
CVD is another popular technique that involves depositing a solid material from a vapor phase. This method is known for producing high-quality films with excellent uniformity.
B. Patterning and Etching
1. Photolithography
Photolithography is a critical process in the manufacturing of thin film resistors, allowing for the precise patterning of resistive materials on substrates.
2. Laser Etching
Laser etching is increasingly used for its ability to create intricate patterns with high precision, enhancing the performance and reliability of thin film resistors.
C. Quality Control Measures
1. Testing and Validation Processes
Manufacturers employ rigorous testing and validation processes to ensure that thin film resistors meet specified performance criteria. This includes electrical testing, thermal cycling, and environmental testing.
2. Standards and Certifications
Compliance with industry standards and certifications, such as ISO and RoHS, is essential for ensuring the quality and reliability of thin film resistors.
VI. Applications of Thin Film Resistors
A. Consumer Electronics
Thin film resistors are commonly used in consumer electronics, including smartphones, tablets, and audio equipment, where precision and low noise are critical.
B. Automotive Industry
In the automotive sector, thin film resistors are employed in various applications, from engine control units to advanced driver-assistance systems (ADAS), where reliability and performance are paramount.
C. Medical Devices
Medical devices, such as diagnostic equipment and monitoring systems, rely on thin film resistors for their accuracy and stability, ensuring patient safety and effective treatment.
D. Telecommunications
Thin film resistors are essential in telecommunications equipment, where they help maintain signal integrity and reduce noise in high-frequency applications.
E. Aerospace and Defense
In aerospace and defense applications, thin film resistors are used in critical systems where performance and reliability are non-negotiable, such as navigation and communication systems.
VII. Future Trends in Thin Film Resistor Technology
A. Miniaturization and Integration
As electronic devices continue to shrink in size, the demand for miniaturized thin film resistors that can be integrated into compact circuits is on the rise.
B. Enhanced Performance Metrics
Future developments will likely focus on enhancing performance metrics, such as lower TCR, higher power ratings, and improved noise characteristics, to meet the demands of advanced applications.
C. Sustainable and Eco-friendly Materials
The push for sustainability will drive research into eco-friendly materials and manufacturing processes, reducing the environmental impact of thin film resistor production.
D. Innovations in Manufacturing Techniques
Advancements in manufacturing techniques, such as additive manufacturing and advanced deposition methods, will enable the production of more complex and high-performance thin film resistors.
VIII. Conclusion
A. Summary of Key Points
Thin film resistors are essential components in modern electronics, offering superior performance characteristics, including high precision, low noise, and excellent temperature stability. Recent advancements in materials and manufacturing processes have further enhanced their capabilities, making them suitable for a wide range of applications.
B. The Role of Thin Film Resistors in Advancing Technology
As technology continues to evolve, thin film resistors will play a critical role in advancing electronic systems, enabling innovations in consumer electronics, automotive, medical devices, telecommunications, and aerospace.
C. Final Thoughts on Future Developments in the Field
The future of thin film resistor technology looks promising, with ongoing research and development aimed at improving performance, sustainability, and integration into next-generation electronic devices. As the demand for high-performance components grows, thin film resistors will remain at the forefront of electronic innovation.
IX. References
A comprehensive list of academic papers, industry reports, and other resources used for research will be provided to support the information presented in this article.
Latest Thin Film Resistor Specifications
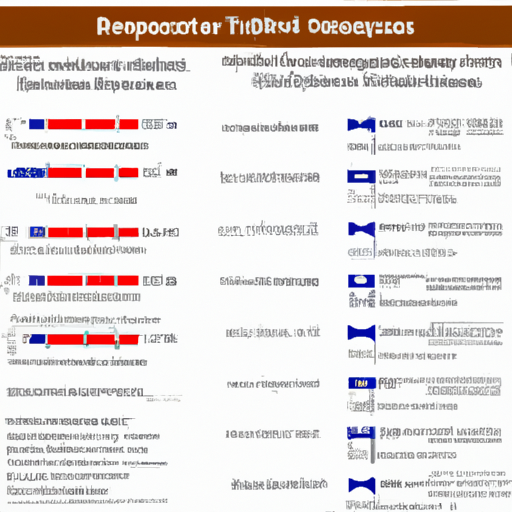
I. Introduction
A. Definition of Thin Film Resistors
Thin film resistors are electronic components that utilize a thin layer of resistive material deposited on a substrate to control the flow of electric current. Unlike traditional resistors, which are typically made from bulk materials, thin film resistors offer superior performance characteristics due to their unique construction and material properties.
B. Importance of Thin Film Resistors in Electronics
Thin film resistors play a crucial role in modern electronics, providing precise resistance values, excellent temperature stability, and low noise characteristics. They are widely used in applications ranging from consumer electronics to aerospace, where reliability and performance are paramount. As technology advances, the demand for high-performance resistors continues to grow, making thin film resistors an essential component in the design of sophisticated electronic systems.
C. Purpose of the Article
This article aims to provide an overview of the latest specifications and advancements in thin film resistors, highlighting their significance in various applications and the ongoing innovations in materials and manufacturing processes.
II. Overview of Thin Film Resistor Technology
A. Historical Background
1. Development of Thin Film Technology
The development of thin film technology began in the mid-20th century, driven by the need for smaller, more efficient electronic components. Early thin film resistors were primarily used in military and aerospace applications, where performance and reliability were critical.
2. Evolution of Materials and Manufacturing Processes
Over the years, advancements in materials science and manufacturing techniques have led to the creation of more sophisticated thin film resistors. The introduction of new materials, such as tantalum nitride and nickel-chromium, has improved the performance and reliability of these components, making them suitable for a wider range of applications.
B. Basic Principles of Operation
1. Structure and Composition
Thin film resistors consist of a thin layer of resistive material, typically ranging from a few nanometers to several micrometers in thickness, deposited on a substrate. The choice of substrate material, such as ceramic or silicon, can significantly impact the resistor's performance.
2. Mechanism of Resistance in Thin Films
The resistance in thin film resistors arises from the interaction of electrons with the resistive material. The thinness of the film allows for a more uniform distribution of current, resulting in lower noise and improved stability compared to traditional resistors.
III. Key Specifications of Thin Film Resistors
A. Resistance Values
1. Range of Resistance Values Available
Thin film resistors are available in a wide range of resistance values, typically from a few ohms to several megaohms. This versatility makes them suitable for various applications, from precision measurement devices to high-frequency circuits.
2. Tolerance Levels and Their Significance
Tolerance levels indicate the accuracy of the resistance value, with thin film resistors offering tolerances as low as ±0.01%. This high level of precision is essential in applications where even minor variations in resistance can lead to significant performance issues.
B. Temperature Coefficient of Resistance (TCR)
1. Definition and Importance
The temperature coefficient of resistance (TCR) measures how much a resistor's resistance changes with temperature. A low TCR is crucial for applications requiring stable performance across varying temperatures, such as in automotive and aerospace systems.
2. Latest Advancements in TCR Specifications
Recent advancements have led to thin film resistors with TCR values as low as ±5 ppm/°C, significantly enhancing their performance in temperature-sensitive applications.
C. Power Rating
1. Explanation of Power Handling Capabilities
Power rating refers to the maximum power a resistor can dissipate without overheating. Thin film resistors typically have power ratings ranging from a few milliwatts to several watts, depending on their size and construction.
2. Comparison with Other Resistor Types
Compared to thick film and wire-wound resistors, thin film resistors generally offer higher power ratings in smaller packages, making them ideal for compact electronic designs.
D. Voltage Rating
1. Maximum Voltage Specifications
Voltage rating indicates the maximum voltage a resistor can withstand without failure. Thin film resistors can handle voltages ranging from a few volts to several hundred volts, depending on their design and materials.
2. Impact on Circuit Design and Performance
Understanding voltage ratings is crucial for circuit designers, as exceeding these limits can lead to resistor failure and circuit malfunction. Thin film resistors' high voltage ratings make them suitable for high-performance applications.
E. Noise Characteristics
1. Types of Noise in Resistors
Resistors can generate various types of noise, including thermal noise, shot noise, and flicker noise. Thin film resistors are known for their low noise characteristics, making them ideal for sensitive applications such as audio and precision measurement.
2. Latest Specifications for Noise Performance
Recent developments have led to thin film resistors with noise levels as low as -40 dB, significantly improving the performance of circuits where noise can adversely affect signal integrity.
IV. Materials Used in Thin Film Resistors
A. Common Materials
1. Nickel-Chromium (NiCr)
Nickel-chromium is one of the most widely used materials for thin film resistors due to its excellent stability and resistance to oxidation.
2. Tantalum Nitride (TaN)
Tantalum nitride is gaining popularity for its high thermal stability and low TCR, making it suitable for high-performance applications.
3. Other Emerging Materials
Research is ongoing into alternative materials, such as graphene and carbon nanotubes, which promise even better performance characteristics.
B. Impact of Material Choice on Performance
1. Stability and Reliability
The choice of material directly impacts the stability and reliability of thin film resistors. High-quality materials ensure consistent performance over time, even in challenging environments.
2. Environmental Considerations
As environmental concerns grow, manufacturers are exploring eco-friendly materials and processes to reduce the environmental impact of thin film resistor production.
V. Manufacturing Processes
A. Deposition Techniques
1. Sputtering
Sputtering is a widely used deposition technique that involves ejecting material from a target onto a substrate, creating a thin film. This method allows for precise control over film thickness and composition.
2. Chemical Vapor Deposition (CVD)
CVD is another popular technique that involves depositing a solid material from a vapor phase. This method is known for producing high-quality films with excellent uniformity.
B. Patterning and Etching
1. Photolithography
Photolithography is a critical process in the manufacturing of thin film resistors, allowing for the precise patterning of resistive materials on substrates.
2. Laser Etching
Laser etching is increasingly used for its ability to create intricate patterns with high precision, enhancing the performance and reliability of thin film resistors.
C. Quality Control Measures
1. Testing and Validation Processes
Manufacturers employ rigorous testing and validation processes to ensure that thin film resistors meet specified performance criteria. This includes electrical testing, thermal cycling, and environmental testing.
2. Standards and Certifications
Compliance with industry standards and certifications, such as ISO and RoHS, is essential for ensuring the quality and reliability of thin film resistors.
VI. Applications of Thin Film Resistors
A. Consumer Electronics
Thin film resistors are commonly used in consumer electronics, including smartphones, tablets, and audio equipment, where precision and low noise are critical.
B. Automotive Industry
In the automotive sector, thin film resistors are employed in various applications, from engine control units to advanced driver-assistance systems (ADAS), where reliability and performance are paramount.
C. Medical Devices
Medical devices, such as diagnostic equipment and monitoring systems, rely on thin film resistors for their accuracy and stability, ensuring patient safety and effective treatment.
D. Telecommunications
Thin film resistors are essential in telecommunications equipment, where they help maintain signal integrity and reduce noise in high-frequency applications.
E. Aerospace and Defense
In aerospace and defense applications, thin film resistors are used in critical systems where performance and reliability are non-negotiable, such as navigation and communication systems.
VII. Future Trends in Thin Film Resistor Technology
A. Miniaturization and Integration
As electronic devices continue to shrink in size, the demand for miniaturized thin film resistors that can be integrated into compact circuits is on the rise.
B. Enhanced Performance Metrics
Future developments will likely focus on enhancing performance metrics, such as lower TCR, higher power ratings, and improved noise characteristics, to meet the demands of advanced applications.
C. Sustainable and Eco-friendly Materials
The push for sustainability will drive research into eco-friendly materials and manufacturing processes, reducing the environmental impact of thin film resistor production.
D. Innovations in Manufacturing Techniques
Advancements in manufacturing techniques, such as additive manufacturing and advanced deposition methods, will enable the production of more complex and high-performance thin film resistors.
VIII. Conclusion
A. Summary of Key Points
Thin film resistors are essential components in modern electronics, offering superior performance characteristics, including high precision, low noise, and excellent temperature stability. Recent advancements in materials and manufacturing processes have further enhanced their capabilities, making them suitable for a wide range of applications.
B. The Role of Thin Film Resistors in Advancing Technology
As technology continues to evolve, thin film resistors will play a critical role in advancing electronic systems, enabling innovations in consumer electronics, automotive, medical devices, telecommunications, and aerospace.
C. Final Thoughts on Future Developments in the Field
The future of thin film resistor technology looks promising, with ongoing research and development aimed at improving performance, sustainability, and integration into next-generation electronic devices. As the demand for high-performance components grows, thin film resistors will remain at the forefront of electronic innovation.
IX. References
A comprehensive list of academic papers, industry reports, and other resources used for research will be provided to support the information presented in this article.