What is the Production Process of Mainstream Resistor Wiring Diagram?
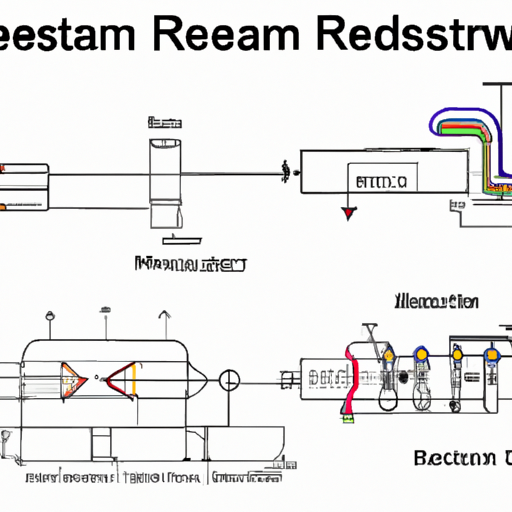
I. Introduction
Resistors are fundamental components in electronic circuits, serving the crucial role of controlling current flow. They are essential for protecting sensitive components, dividing voltages, and managing signal levels. As technology advances, the complexity of electronic devices increases, making the need for accurate resistor wiring diagrams more critical than ever. These diagrams serve as blueprints for engineers and technicians, guiding the assembly and integration of resistors into various applications. This blog post will explore the production process of mainstream resistor wiring diagrams, detailing each step from initial design to manufacturing and integration.
II. Understanding Resistors
A. Types of Resistors
Resistors come in various types, each designed for specific applications:
1. **Fixed Resistors**: These resistors have a constant resistance value and are widely used in circuits where precise resistance is required.
2. **Variable Resistors**: Also known as potentiometers, these allow for adjustable resistance, making them ideal for applications like volume controls in audio equipment.
3. **Specialty Resistors**: This category includes thermistors, photoresistors, and others that respond to environmental changes, providing unique functionalities.
B. Functionality of Resistors in Circuits
Resistors play a vital role in controlling the flow of electric current. By providing resistance, they help to limit current, divide voltages, and dissipate energy as heat. This functionality is crucial in protecting sensitive components from damage and ensuring the proper operation of electronic devices.
C. Common Applications of Resistors
Resistors are ubiquitous in electronic devices, from simple household appliances to complex industrial machinery. They are used in power supplies, signal processing, and even in digital circuits, highlighting their versatility and importance in modern technology.
III. Components of a Resistor Wiring Diagram
A. Symbols Used in Wiring Diagrams
Wiring diagrams utilize standardized symbols to represent various components, including resistors. Understanding these symbols is essential for anyone working with electronic circuits, as they provide a universal language for engineers and technicians.
B. Layout and Design Considerations
The layout of a wiring diagram must be clear and logical, allowing for easy interpretation. Factors such as component placement, connection paths, and labeling are crucial for ensuring that the diagram effectively communicates the intended design.
C. Importance of Accurate Diagrams in Production
Accurate wiring diagrams are essential for the successful production and assembly of electronic devices. They serve as a reference for technicians, helping to prevent errors and ensuring that components are connected correctly.
IV. The Production Process of Resistor Wiring Diagrams
A. Initial Design Phase
1. Conceptualization
The production of a resistor wiring diagram begins with conceptualization. Engineers and designers collaborate to outline the circuit's purpose, functionality, and requirements. This phase involves brainstorming and sketching initial ideas.
2. Software Tools Used (e.g., CAD)
Once the concept is established, designers utilize computer-aided design (CAD) software to create detailed wiring diagrams. These tools allow for precise measurements, easy modifications, and the ability to simulate circuit behavior.
B. Component Selection
1. Choosing Resistor Types
Selecting the appropriate resistor types is critical to the circuit's performance. Engineers must consider factors such as resistance value, tolerance, power rating, and temperature coefficient.
2. Sourcing Materials
After selecting the resistor types, the next step is sourcing materials. This involves identifying reliable suppliers and ensuring that the materials meet industry standards and specifications.
C. Drafting the Wiring Diagram
1. Creating the Layout
With the components selected, the designer drafts the wiring diagram. This process involves arranging the components logically and ensuring that the connections are clear and easy to follow.
2. Incorporating Electrical Standards
Wiring diagrams must adhere to electrical standards and regulations. This ensures safety and compatibility with existing systems, making it essential for designers to stay updated on industry guidelines.
D. Review and Revision
1. Peer Review Process
Once the initial draft is complete, it undergoes a peer review process. Colleagues and experts evaluate the diagram for accuracy, clarity, and adherence to standards.
2. Testing for Accuracy and Functionality
After revisions, the diagram is tested to ensure that it accurately represents the intended circuit. This may involve simulations or prototyping to verify that the design functions as expected.
V. Manufacturing of Resistors
A. Material Preparation
1. Conductive Materials (Carbon, Metal Film, etc.)
The manufacturing process begins with preparing conductive materials. Common materials include carbon, metal film, and wire, each chosen based on the desired resistor characteristics.
2. Insulating Materials
Insulating materials are also essential, as they prevent unwanted current flow and protect the resistor from environmental factors. Common insulators include ceramic and epoxy.
B. Fabrication Techniques
1. Thin Film vs. Thick Film Technology
Resistors can be manufactured using thin film or thick film technology. Thin film resistors offer higher precision and stability, while thick film resistors are more cost-effective for mass production.
2. Wirewound Resistors
Wirewound resistors are made by winding a wire around a core. This technique allows for high power ratings and is commonly used in applications requiring high precision.
C. Quality Control Measures
1. Testing for Resistance Values
Quality control is critical in resistor manufacturing. Each resistor is tested for its resistance value to ensure it meets specifications. This may involve automated testing equipment for efficiency.
2. Ensuring Durability and Reliability
Durability and reliability are also assessed through various tests, including temperature cycling and humidity exposure, to ensure that the resistors can withstand real-world conditions.
VI. Integration of Wiring Diagrams in Production
A. Role of Diagrams in Assembly
Wiring diagrams play a crucial role in the assembly process. They guide technicians in connecting components correctly, ensuring that the final product functions as intended.
B. Training for Technicians and Engineers
Proper training is essential for technicians and engineers to interpret wiring diagrams effectively. This training helps prevent errors during assembly and enhances overall production efficiency.
C. Importance of Documentation for Future Reference
Accurate documentation of wiring diagrams is vital for future reference. This documentation aids in troubleshooting, maintenance, and potential upgrades, ensuring the longevity of electronic devices.
VII. Challenges in the Production Process
A. Common Issues Faced
1. Design Flaws
Design flaws can lead to significant issues during production, resulting in wasted materials and time. Identifying and addressing these flaws early in the process is crucial.
2. Material Shortages
Material shortages can disrupt the production process, leading to delays and increased costs. Establishing strong supplier relationships can help mitigate this risk.
B. Solutions and Best Practices
1. Continuous Improvement Strategies
Implementing continuous improvement strategies, such as regular reviews and updates to processes, can enhance efficiency and reduce errors in production.
2. Use of Simulation Software
Simulation software can help identify potential issues in wiring diagrams before production begins, allowing for adjustments and improvements to be made proactively.
VIII. Future Trends in Resistor Production and Wiring Diagrams
A. Advances in Technology
1. Automation in Manufacturing
Automation is transforming resistor manufacturing, increasing efficiency and reducing labor costs. Automated systems can handle repetitive tasks, allowing engineers to focus on design and innovation.
2. Smart Resistors and IoT Integration
The rise of the Internet of Things (IoT) is leading to the development of smart resistors that can communicate with other devices. This integration opens up new possibilities for monitoring and controlling electronic systems.
B. Evolving Standards and Regulations
As technology advances, so do the standards and regulations governing resistor production. Staying informed about these changes is essential for manufacturers to ensure compliance and maintain product quality.
C. Sustainability in Resistor Production
Sustainability is becoming increasingly important in the manufacturing sector. Companies are exploring eco-friendly materials and processes to reduce their environmental impact and meet consumer demand for sustainable products.
IX. Conclusion
In conclusion, resistor wiring diagrams are essential tools in the production process of electronic devices. They provide a clear and accurate representation of circuit designs, guiding technicians and engineers in assembly and integration. The production process involves several critical steps, from initial design to manufacturing and quality control. As technology continues to evolve, the industry must adapt to new challenges and opportunities, ensuring that resistor production remains efficient, reliable, and sustainable. The future of resistor technology holds exciting possibilities, with advancements in automation, smart devices, and eco-friendly practices paving the way for innovation in the field.
What is the Production Process of Mainstream Resistor Wiring Diagram?
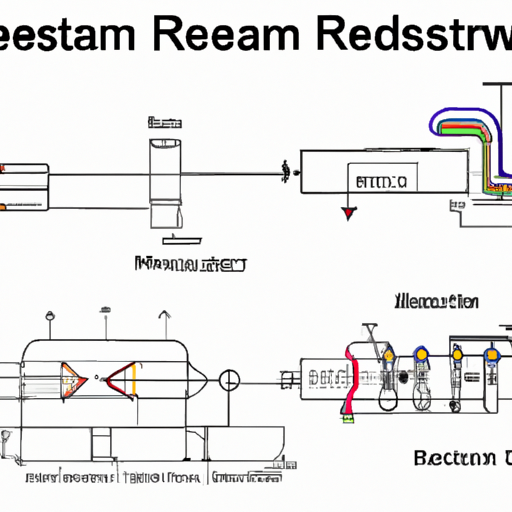
I. Introduction
Resistors are fundamental components in electronic circuits, serving the crucial role of controlling current flow. They are essential for protecting sensitive components, dividing voltages, and managing signal levels. As technology advances, the complexity of electronic devices increases, making the need for accurate resistor wiring diagrams more critical than ever. These diagrams serve as blueprints for engineers and technicians, guiding the assembly and integration of resistors into various applications. This blog post will explore the production process of mainstream resistor wiring diagrams, detailing each step from initial design to manufacturing and integration.
II. Understanding Resistors
A. Types of Resistors
Resistors come in various types, each designed for specific applications:
1. **Fixed Resistors**: These resistors have a constant resistance value and are widely used in circuits where precise resistance is required.
2. **Variable Resistors**: Also known as potentiometers, these allow for adjustable resistance, making them ideal for applications like volume controls in audio equipment.
3. **Specialty Resistors**: This category includes thermistors, photoresistors, and others that respond to environmental changes, providing unique functionalities.
B. Functionality of Resistors in Circuits
Resistors play a vital role in controlling the flow of electric current. By providing resistance, they help to limit current, divide voltages, and dissipate energy as heat. This functionality is crucial in protecting sensitive components from damage and ensuring the proper operation of electronic devices.
C. Common Applications of Resistors
Resistors are ubiquitous in electronic devices, from simple household appliances to complex industrial machinery. They are used in power supplies, signal processing, and even in digital circuits, highlighting their versatility and importance in modern technology.
III. Components of a Resistor Wiring Diagram
A. Symbols Used in Wiring Diagrams
Wiring diagrams utilize standardized symbols to represent various components, including resistors. Understanding these symbols is essential for anyone working with electronic circuits, as they provide a universal language for engineers and technicians.
B. Layout and Design Considerations
The layout of a wiring diagram must be clear and logical, allowing for easy interpretation. Factors such as component placement, connection paths, and labeling are crucial for ensuring that the diagram effectively communicates the intended design.
C. Importance of Accurate Diagrams in Production
Accurate wiring diagrams are essential for the successful production and assembly of electronic devices. They serve as a reference for technicians, helping to prevent errors and ensuring that components are connected correctly.
IV. The Production Process of Resistor Wiring Diagrams
A. Initial Design Phase
1. Conceptualization
The production of a resistor wiring diagram begins with conceptualization. Engineers and designers collaborate to outline the circuit's purpose, functionality, and requirements. This phase involves brainstorming and sketching initial ideas.
2. Software Tools Used (e.g., CAD)
Once the concept is established, designers utilize computer-aided design (CAD) software to create detailed wiring diagrams. These tools allow for precise measurements, easy modifications, and the ability to simulate circuit behavior.
B. Component Selection
1. Choosing Resistor Types
Selecting the appropriate resistor types is critical to the circuit's performance. Engineers must consider factors such as resistance value, tolerance, power rating, and temperature coefficient.
2. Sourcing Materials
After selecting the resistor types, the next step is sourcing materials. This involves identifying reliable suppliers and ensuring that the materials meet industry standards and specifications.
C. Drafting the Wiring Diagram
1. Creating the Layout
With the components selected, the designer drafts the wiring diagram. This process involves arranging the components logically and ensuring that the connections are clear and easy to follow.
2. Incorporating Electrical Standards
Wiring diagrams must adhere to electrical standards and regulations. This ensures safety and compatibility with existing systems, making it essential for designers to stay updated on industry guidelines.
D. Review and Revision
1. Peer Review Process
Once the initial draft is complete, it undergoes a peer review process. Colleagues and experts evaluate the diagram for accuracy, clarity, and adherence to standards.
2. Testing for Accuracy and Functionality
After revisions, the diagram is tested to ensure that it accurately represents the intended circuit. This may involve simulations or prototyping to verify that the design functions as expected.
V. Manufacturing of Resistors
A. Material Preparation
1. Conductive Materials (Carbon, Metal Film, etc.)
The manufacturing process begins with preparing conductive materials. Common materials include carbon, metal film, and wire, each chosen based on the desired resistor characteristics.
2. Insulating Materials
Insulating materials are also essential, as they prevent unwanted current flow and protect the resistor from environmental factors. Common insulators include ceramic and epoxy.
B. Fabrication Techniques
1. Thin Film vs. Thick Film Technology
Resistors can be manufactured using thin film or thick film technology. Thin film resistors offer higher precision and stability, while thick film resistors are more cost-effective for mass production.
2. Wirewound Resistors
Wirewound resistors are made by winding a wire around a core. This technique allows for high power ratings and is commonly used in applications requiring high precision.
C. Quality Control Measures
1. Testing for Resistance Values
Quality control is critical in resistor manufacturing. Each resistor is tested for its resistance value to ensure it meets specifications. This may involve automated testing equipment for efficiency.
2. Ensuring Durability and Reliability
Durability and reliability are also assessed through various tests, including temperature cycling and humidity exposure, to ensure that the resistors can withstand real-world conditions.
VI. Integration of Wiring Diagrams in Production
A. Role of Diagrams in Assembly
Wiring diagrams play a crucial role in the assembly process. They guide technicians in connecting components correctly, ensuring that the final product functions as intended.
B. Training for Technicians and Engineers
Proper training is essential for technicians and engineers to interpret wiring diagrams effectively. This training helps prevent errors during assembly and enhances overall production efficiency.
C. Importance of Documentation for Future Reference
Accurate documentation of wiring diagrams is vital for future reference. This documentation aids in troubleshooting, maintenance, and potential upgrades, ensuring the longevity of electronic devices.
VII. Challenges in the Production Process
A. Common Issues Faced
1. Design Flaws
Design flaws can lead to significant issues during production, resulting in wasted materials and time. Identifying and addressing these flaws early in the process is crucial.
2. Material Shortages
Material shortages can disrupt the production process, leading to delays and increased costs. Establishing strong supplier relationships can help mitigate this risk.
B. Solutions and Best Practices
1. Continuous Improvement Strategies
Implementing continuous improvement strategies, such as regular reviews and updates to processes, can enhance efficiency and reduce errors in production.
2. Use of Simulation Software
Simulation software can help identify potential issues in wiring diagrams before production begins, allowing for adjustments and improvements to be made proactively.
VIII. Future Trends in Resistor Production and Wiring Diagrams
A. Advances in Technology
1. Automation in Manufacturing
Automation is transforming resistor manufacturing, increasing efficiency and reducing labor costs. Automated systems can handle repetitive tasks, allowing engineers to focus on design and innovation.
2. Smart Resistors and IoT Integration
The rise of the Internet of Things (IoT) is leading to the development of smart resistors that can communicate with other devices. This integration opens up new possibilities for monitoring and controlling electronic systems.
B. Evolving Standards and Regulations
As technology advances, so do the standards and regulations governing resistor production. Staying informed about these changes is essential for manufacturers to ensure compliance and maintain product quality.
C. Sustainability in Resistor Production
Sustainability is becoming increasingly important in the manufacturing sector. Companies are exploring eco-friendly materials and processes to reduce their environmental impact and meet consumer demand for sustainable products.
IX. Conclusion
In conclusion, resistor wiring diagrams are essential tools in the production process of electronic devices. They provide a clear and accurate representation of circuit designs, guiding technicians and engineers in assembly and integration. The production process involves several critical steps, from initial design to manufacturing and quality control. As technology continues to evolve, the industry must adapt to new challenges and opportunities, ensuring that resistor production remains efficient, reliable, and sustainable. The future of resistor technology holds exciting possibilities, with advancements in automation, smart devices, and eco-friendly practices paving the way for innovation in the field.