Common Production Processes for Capacitors
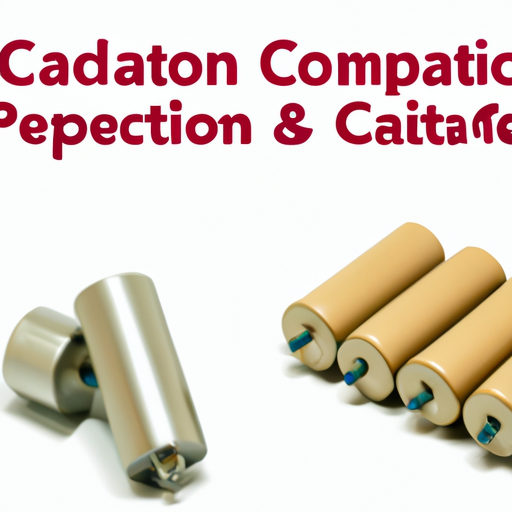
I. Introduction
Capacitors are essential components in modern electronic devices, serving as energy storage units that can release energy quickly when needed. They play a crucial role in various applications, from filtering signals in audio equipment to stabilizing voltage in power supplies. Understanding the production processes of capacitors is vital for appreciating their functionality and reliability in electronic systems. This blog post will explore the common production processes for capacitors, detailing the various types, general manufacturing steps, and specific processes for each capacitor type.
II. Types of Capacitors
Capacitors come in several types, each designed for specific applications and performance characteristics. The most common types include:
A. Ceramic Capacitors
Ceramic capacitors are widely used due to their small size, low cost, and stability. They are often found in high-frequency applications.
B. Electrolytic Capacitors
These capacitors are known for their high capacitance values and are typically used in power supply circuits. They are polarized, meaning they have a positive and negative terminal.
C. Film Capacitors
Film capacitors use a thin plastic film as the dielectric material. They are known for their reliability and are often used in audio and high-frequency applications.
D. Tantalum Capacitors
Tantalum capacitors are known for their high capacitance in a small package. They are often used in applications where space is limited.
E. Supercapacitors
Supercapacitors, or ultracapacitors, have a very high capacitance and are used for energy storage applications, such as in electric vehicles and renewable energy systems.
III. General Production Processes
The production of capacitors involves several general processes that apply across different types. These processes ensure that the capacitors meet the required specifications and quality standards.
A. Raw Material Selection
1. Types of Materials Used
The production of capacitors begins with the selection of raw materials. The choice of dielectric materials, electrodes, and electrolytes is critical. Common materials include ceramic powders for ceramic capacitors, aluminum foil for electrolytic capacitors, and plastic films for film capacitors.
2. Quality Control Measures
Quality control is essential at this stage to ensure that the materials meet the required specifications. This may involve testing for purity, dielectric strength, and other relevant properties.
B. Component Fabrication
1. Dielectric Materials
The dielectric material is the insulating layer that separates the capacitor's plates. The fabrication process varies depending on the type of capacitor but generally involves shaping the dielectric material into the desired form.
2. Electrodes
Electrodes are typically made from conductive materials such as aluminum, tantalum, or metalized films. The production process includes cutting, shaping, and sometimes coating the electrodes to enhance their performance.
3. Leads and Terminals
Leads and terminals are essential for connecting the capacitor to a circuit. They are usually made from conductive metals and are attached to the capacitor during the assembly process.
IV. Specific Production Processes by Capacitor Type
Each type of capacitor has its unique production processes, which are tailored to its specific requirements.
A. Ceramic Capacitors
1. Powder Preparation
The production of ceramic capacitors begins with the preparation of ceramic powders. These powders are mixed with additives to achieve the desired dielectric properties.
2. Pressing and Sintering
The prepared powder is then pressed into the desired shape and sintered at high temperatures to form a solid ceramic body. This process enhances the dielectric properties and mechanical strength of the capacitor.
3. Electrode Application
After sintering, electrodes are applied to the ceramic body. This can be done through various methods, including screen printing or sputtering.
4. Glazing and Firing
Finally, the capacitor is glazed and fired to improve its surface finish and protect it from environmental factors.
B. Electrolytic Capacitors
1. Anodization of Aluminum Foil
Electrolytic capacitors start with the anodization of aluminum foil, which creates a thin oxide layer that serves as the dielectric. This process is crucial for achieving the high capacitance values characteristic of these capacitors.
2. Electrolyte Filling
Once the anodization is complete, the capacitor is filled with an electrolyte solution, which enhances its performance.
3. Sealing and Packaging
The final steps involve sealing the capacitor to prevent leakage and packaging it for distribution.
C. Film Capacitors
1. Film Extrusion
Film capacitors begin with the extrusion of plastic films, which are then stretched to improve their dielectric properties.
2. Metallization
The films are metallized by depositing a thin layer of metal, which forms the electrodes.
3. Winding and Cutting
The metallized films are wound into a cylindrical shape and cut to the desired size, ready for assembly.
D. Tantalum Capacitors
1. Tantalum Powder Preparation
Tantalum capacitors start with the preparation of tantalum powder, which is then compacted and sintered to form the capacitor's anode.
2. Sintering and Forming
The sintering process is critical for achieving the desired electrical properties. After sintering, the tantalum anode is formed into the required shape.
3. Electrolyte Application
An electrolyte is then applied to the tantalum anode, completing the capacitor's assembly.
E. Supercapacitors
1. Electrode Preparation
Supercapacitors require specialized electrodes, often made from activated carbon. The preparation involves creating a porous structure to maximize surface area.
2. Electrolyte Selection
The choice of electrolyte is crucial for the performance of supercapacitors. Various electrolytes can be used, including aqueous and organic solutions.
3. Assembly and Packaging
Finally, the electrodes and electrolyte are assembled into a cell, which is then packaged for use in various applications.
V. Quality Control and Testing
Quality control is a critical aspect of capacitor production. Manufacturers implement several measures to ensure that the capacitors meet industry standards.
A. In-process Quality Checks
During production, in-process checks are conducted to monitor the quality of materials and components. This includes testing for defects and ensuring that specifications are met.
B. Final Testing Procedures
Once the capacitors are assembled, they undergo final testing to verify their performance characteristics, such as capacitance, voltage rating, and leakage current.
C. Reliability Testing
Reliability testing is essential to ensure that capacitors can withstand the conditions they will encounter in real-world applications. This may involve accelerated aging tests and environmental stress tests.
VI. Environmental Considerations
As the electronics industry grows, so does the need for sustainable practices in capacitor production.
A. Waste Management
Manufacturers are increasingly focusing on waste management practices to minimize the environmental impact of production processes.
B. Recycling of Materials
Recycling initiatives are being implemented to recover valuable materials from used capacitors, reducing the need for new raw materials.
C. Compliance with Regulations
Manufacturers must comply with environmental regulations, such as the Restriction of Hazardous Substances (RoHS) directive, to ensure that their products are safe for consumers and the environment.
VII. Conclusion
In summary, the production processes for capacitors are complex and varied, depending on the type of capacitor being manufactured. From raw material selection to final testing, each step is crucial for ensuring the performance and reliability of these essential components. As technology advances, the capacitor manufacturing industry is likely to see innovations that improve efficiency, reduce environmental impact, and enhance performance. Understanding these processes not only highlights the importance of capacitors in electronic devices but also underscores the need for continuous improvement and innovation in capacitor technology.
VIII. References
- Academic journals on capacitor technology and manufacturing processes.
- Industry reports detailing trends and advancements in capacitor production.
- Manufacturer guidelines and specifications for various types of capacitors.
This comprehensive overview of capacitor production processes provides valuable insights into the intricate world of electronics manufacturing, emphasizing the importance of quality, sustainability, and innovation in the industry.
Common Production Processes for Capacitors
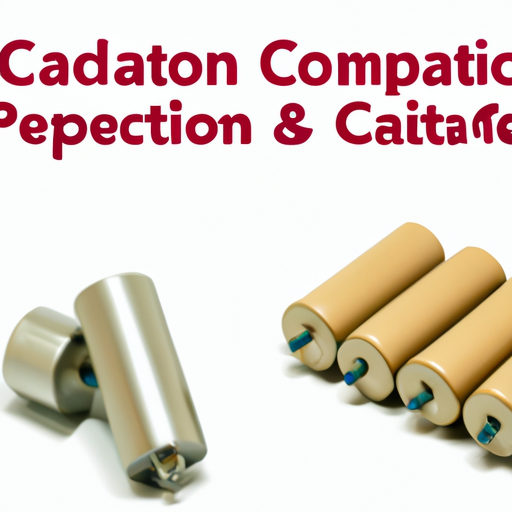
I. Introduction
Capacitors are essential components in modern electronic devices, serving as energy storage units that can release energy quickly when needed. They play a crucial role in various applications, from filtering signals in audio equipment to stabilizing voltage in power supplies. Understanding the production processes of capacitors is vital for appreciating their functionality and reliability in electronic systems. This blog post will explore the common production processes for capacitors, detailing the various types, general manufacturing steps, and specific processes for each capacitor type.
II. Types of Capacitors
Capacitors come in several types, each designed for specific applications and performance characteristics. The most common types include:
A. Ceramic Capacitors
Ceramic capacitors are widely used due to their small size, low cost, and stability. They are often found in high-frequency applications.
B. Electrolytic Capacitors
These capacitors are known for their high capacitance values and are typically used in power supply circuits. They are polarized, meaning they have a positive and negative terminal.
C. Film Capacitors
Film capacitors use a thin plastic film as the dielectric material. They are known for their reliability and are often used in audio and high-frequency applications.
D. Tantalum Capacitors
Tantalum capacitors are known for their high capacitance in a small package. They are often used in applications where space is limited.
E. Supercapacitors
Supercapacitors, or ultracapacitors, have a very high capacitance and are used for energy storage applications, such as in electric vehicles and renewable energy systems.
III. General Production Processes
The production of capacitors involves several general processes that apply across different types. These processes ensure that the capacitors meet the required specifications and quality standards.
A. Raw Material Selection
1. Types of Materials Used
The production of capacitors begins with the selection of raw materials. The choice of dielectric materials, electrodes, and electrolytes is critical. Common materials include ceramic powders for ceramic capacitors, aluminum foil for electrolytic capacitors, and plastic films for film capacitors.
2. Quality Control Measures
Quality control is essential at this stage to ensure that the materials meet the required specifications. This may involve testing for purity, dielectric strength, and other relevant properties.
B. Component Fabrication
1. Dielectric Materials
The dielectric material is the insulating layer that separates the capacitor's plates. The fabrication process varies depending on the type of capacitor but generally involves shaping the dielectric material into the desired form.
2. Electrodes
Electrodes are typically made from conductive materials such as aluminum, tantalum, or metalized films. The production process includes cutting, shaping, and sometimes coating the electrodes to enhance their performance.
3. Leads and Terminals
Leads and terminals are essential for connecting the capacitor to a circuit. They are usually made from conductive metals and are attached to the capacitor during the assembly process.
IV. Specific Production Processes by Capacitor Type
Each type of capacitor has its unique production processes, which are tailored to its specific requirements.
A. Ceramic Capacitors
1. Powder Preparation
The production of ceramic capacitors begins with the preparation of ceramic powders. These powders are mixed with additives to achieve the desired dielectric properties.
2. Pressing and Sintering
The prepared powder is then pressed into the desired shape and sintered at high temperatures to form a solid ceramic body. This process enhances the dielectric properties and mechanical strength of the capacitor.
3. Electrode Application
After sintering, electrodes are applied to the ceramic body. This can be done through various methods, including screen printing or sputtering.
4. Glazing and Firing
Finally, the capacitor is glazed and fired to improve its surface finish and protect it from environmental factors.
B. Electrolytic Capacitors
1. Anodization of Aluminum Foil
Electrolytic capacitors start with the anodization of aluminum foil, which creates a thin oxide layer that serves as the dielectric. This process is crucial for achieving the high capacitance values characteristic of these capacitors.
2. Electrolyte Filling
Once the anodization is complete, the capacitor is filled with an electrolyte solution, which enhances its performance.
3. Sealing and Packaging
The final steps involve sealing the capacitor to prevent leakage and packaging it for distribution.
C. Film Capacitors
1. Film Extrusion
Film capacitors begin with the extrusion of plastic films, which are then stretched to improve their dielectric properties.
2. Metallization
The films are metallized by depositing a thin layer of metal, which forms the electrodes.
3. Winding and Cutting
The metallized films are wound into a cylindrical shape and cut to the desired size, ready for assembly.
D. Tantalum Capacitors
1. Tantalum Powder Preparation
Tantalum capacitors start with the preparation of tantalum powder, which is then compacted and sintered to form the capacitor's anode.
2. Sintering and Forming
The sintering process is critical for achieving the desired electrical properties. After sintering, the tantalum anode is formed into the required shape.
3. Electrolyte Application
An electrolyte is then applied to the tantalum anode, completing the capacitor's assembly.
E. Supercapacitors
1. Electrode Preparation
Supercapacitors require specialized electrodes, often made from activated carbon. The preparation involves creating a porous structure to maximize surface area.
2. Electrolyte Selection
The choice of electrolyte is crucial for the performance of supercapacitors. Various electrolytes can be used, including aqueous and organic solutions.
3. Assembly and Packaging
Finally, the electrodes and electrolyte are assembled into a cell, which is then packaged for use in various applications.
V. Quality Control and Testing
Quality control is a critical aspect of capacitor production. Manufacturers implement several measures to ensure that the capacitors meet industry standards.
A. In-process Quality Checks
During production, in-process checks are conducted to monitor the quality of materials and components. This includes testing for defects and ensuring that specifications are met.
B. Final Testing Procedures
Once the capacitors are assembled, they undergo final testing to verify their performance characteristics, such as capacitance, voltage rating, and leakage current.
C. Reliability Testing
Reliability testing is essential to ensure that capacitors can withstand the conditions they will encounter in real-world applications. This may involve accelerated aging tests and environmental stress tests.
VI. Environmental Considerations
As the electronics industry grows, so does the need for sustainable practices in capacitor production.
A. Waste Management
Manufacturers are increasingly focusing on waste management practices to minimize the environmental impact of production processes.
B. Recycling of Materials
Recycling initiatives are being implemented to recover valuable materials from used capacitors, reducing the need for new raw materials.
C. Compliance with Regulations
Manufacturers must comply with environmental regulations, such as the Restriction of Hazardous Substances (RoHS) directive, to ensure that their products are safe for consumers and the environment.
VII. Conclusion
In summary, the production processes for capacitors are complex and varied, depending on the type of capacitor being manufactured. From raw material selection to final testing, each step is crucial for ensuring the performance and reliability of these essential components. As technology advances, the capacitor manufacturing industry is likely to see innovations that improve efficiency, reduce environmental impact, and enhance performance. Understanding these processes not only highlights the importance of capacitors in electronic devices but also underscores the need for continuous improvement and innovation in capacitor technology.
VIII. References
- Academic journals on capacitor technology and manufacturing processes.
- Industry reports detailing trends and advancements in capacitor production.
- Manufacturer guidelines and specifications for various types of capacitors.
This comprehensive overview of capacitor production processes provides valuable insights into the intricate world of electronics manufacturing, emphasizing the importance of quality, sustainability, and innovation in the industry.