The Production Process of Mainstream Capacitors
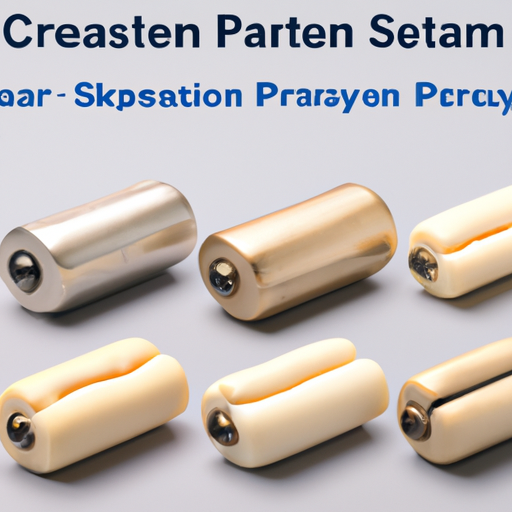
I. Introduction
Capacitors are fundamental components in the world of electronics, serving as energy storage devices that play a crucial role in various applications, from power supply circuits to signal processing. They store electrical energy temporarily and release it when needed, making them essential for stabilizing voltage and filtering signals in electronic devices. As technology advances, the demand for capacitors continues to grow, leading to innovations in their design and production processes. This blog post will explore the production process of mainstream capacitors, detailing the types, raw materials, manufacturing steps, and future trends in capacitor technology.
II. Types of Capacitors
Capacitors come in various types, each designed for specific applications and performance characteristics. The most common types include:
A. Electrolytic Capacitors
Electrolytic capacitors are polarized components that offer high capacitance values in a relatively small package. They are widely used in power supply circuits and audio applications due to their ability to store large amounts of energy.
B. Ceramic Capacitors
Ceramic capacitors are non-polarized and are known for their stability and reliability. They are commonly used in high-frequency applications and are available in various capacitance values.
C. Film Capacitors
Film capacitors utilize a thin plastic film as the dielectric material. They are known for their low loss and high stability, making them suitable for applications in audio equipment and power electronics.
D. Tantalum Capacitors
Tantalum capacitors are known for their high capacitance-to-volume ratio and reliability. They are often used in compact electronic devices, such as smartphones and laptops.
E. Other Types
Other types of capacitors include supercapacitors, which offer high energy density and rapid charge/discharge capabilities, and aluminum capacitors, which are commonly used in power supply circuits.
III. Raw Materials
The production of capacitors begins with the selection of high-quality raw materials. The primary materials used in capacitor production include:
A. Overview of Materials Used in Capacitor Production
1. **Dielectric Materials**: The dielectric material is crucial for a capacitor's performance, as it determines the capacitor's capacitance and voltage rating. Common dielectric materials include ceramic, polyester, polypropylene, and tantalum oxide.
2. **Conductive Materials**: Conductive materials, such as aluminum, tantalum, and copper, are used for the electrodes. The choice of conductive material affects the capacitor's efficiency and performance.
3. **Electrolytes**: In electrolytic capacitors, electrolytes play a vital role in enabling the flow of electric current. Liquid or solid electrolytes are used, depending on the capacitor type.
B. Sourcing and Quality Control of Raw Materials
Sourcing high-quality raw materials is essential for ensuring the reliability and performance of capacitors. Manufacturers often establish relationships with trusted suppliers and implement strict quality control measures to verify the purity and consistency of materials.
IV. Production Process
The production process of capacitors involves several key steps, from design and engineering to manufacturing and quality control.
A. Design and Engineering
1. **Specifications and Requirements**: The first step in the production process is defining the specifications and requirements for the capacitor. This includes determining the desired capacitance, voltage rating, and physical dimensions.
2. **Prototyping and Testing**: Once the specifications are established, prototypes are created and tested to ensure they meet performance criteria. This phase is critical for identifying potential issues before mass production.
B. Manufacturing Steps
1. **Dielectric Layer Preparation**:
- **Material Selection**: The choice of dielectric material is crucial for the capacitor's performance. Manufacturers select materials based on the desired electrical properties and application requirements.
- **Layer Thickness and Uniformity**: The dielectric layer must be applied uniformly to ensure consistent performance. Advanced techniques, such as sputtering or chemical vapor deposition, are often used to achieve the desired thickness.
2. **Electrode Fabrication**:
- **Material Deposition Techniques**: Electrodes are fabricated using various deposition techniques, such as physical vapor deposition (PVD) or chemical vapor deposition (CVD). These methods ensure a high-quality conductive layer.
- **Patterning and Etching**: After deposition, the electrodes are patterned and etched to create the desired shapes and sizes. This step is critical for ensuring proper electrical connections.
3. **Assembly of Capacitor Components**:
- **Layer Stacking**: The dielectric layer and electrodes are stacked together to form the capacitor structure. This process requires precision to ensure proper alignment and contact.
- **Connection of Electrodes**: The electrodes are connected to external leads, allowing the capacitor to be integrated into electronic circuits.
4. **Encapsulation and Packaging**:
- **Protective Coatings**: Capacitors are often coated with protective materials to enhance durability and prevent environmental damage. This step is particularly important for electrolytic capacitors.
- **Final Assembly**: The final assembly involves packaging the capacitors in suitable enclosures, ensuring they are ready for shipment and use in electronic devices.
C. Quality Control
Quality control is a critical aspect of capacitor production, ensuring that each component meets industry standards and performance requirements.
1. **Testing for Electrical Performance**: Capacitors undergo rigorous testing to verify their electrical performance, including capacitance, voltage rating, and leakage current.
2. **Reliability Testing**: Reliability tests, such as temperature cycling and humidity exposure, are conducted to assess the long-term performance of capacitors under various conditions.
3. **Compliance with Industry Standards**: Manufacturers must ensure that their products comply with industry standards, such as those set by the International Electrotechnical Commission (IEC) and the Institute of Electrical and Electronics Engineers (IEEE).
V. Environmental Considerations
As the electronics industry grows, so does the need for sustainable practices in capacitor production.
A. Sustainable Practices in Capacitor Production
Manufacturers are increasingly adopting sustainable practices, such as reducing waste, optimizing energy consumption, and using eco-friendly materials. These efforts not only benefit the environment but also enhance the company's reputation.
B. Recycling and Disposal of Capacitors
Proper recycling and disposal of capacitors are essential to minimize environmental impact. Many manufacturers are exploring ways to recycle materials from old capacitors, reducing the need for new raw materials.
C. Regulatory Compliance and Environmental Impact
Compliance with environmental regulations is crucial for capacitor manufacturers. This includes adhering to laws regarding hazardous materials and waste management, ensuring that production processes do not harm the environment.
VI. Innovations in Capacitor Technology
The capacitor industry is continually evolving, driven by advancements in materials and technology.
A. Advances in Materials and Design
Innovations in dielectric materials and electrode design are leading to capacitors with improved performance characteristics, such as higher capacitance values and lower equivalent series resistance (ESR).
B. Impact of Technology on Production Efficiency
Automation and advanced manufacturing techniques are enhancing production efficiency, reducing costs, and improving product quality. Technologies such as machine learning and artificial intelligence are being integrated into the production process to optimize operations.
C. Future Trends in Capacitor Manufacturing
The future of capacitor manufacturing is likely to be shaped by trends such as miniaturization, increased energy density, and the development of new materials, such as graphene and nanomaterials. These advancements will enable the production of capacitors that meet the demands of next-generation electronic devices.
VII. Conclusion
In summary, the production process of mainstream capacitors is a complex and multifaceted endeavor that involves careful consideration of materials, design, and manufacturing techniques. Capacitors play a vital role in modern electronics, and as technology continues to advance, the demand for innovative and efficient capacitor solutions will only grow. By embracing sustainable practices and investing in research and development, the capacitor industry can ensure a bright future, contributing to the ongoing evolution of electronic devices and systems.
The Production Process of Mainstream Capacitors
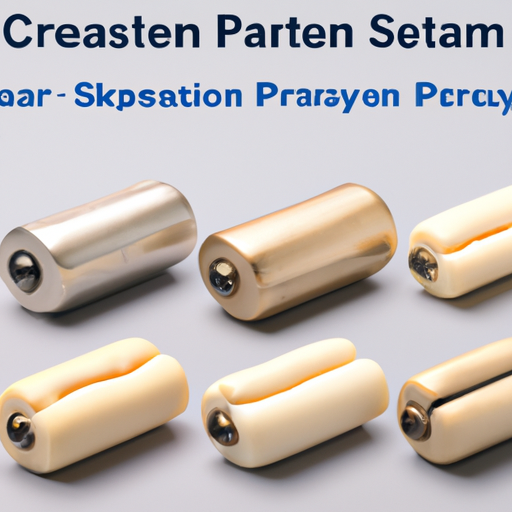
I. Introduction
Capacitors are fundamental components in the world of electronics, serving as energy storage devices that play a crucial role in various applications, from power supply circuits to signal processing. They store electrical energy temporarily and release it when needed, making them essential for stabilizing voltage and filtering signals in electronic devices. As technology advances, the demand for capacitors continues to grow, leading to innovations in their design and production processes. This blog post will explore the production process of mainstream capacitors, detailing the types, raw materials, manufacturing steps, and future trends in capacitor technology.
II. Types of Capacitors
Capacitors come in various types, each designed for specific applications and performance characteristics. The most common types include:
A. Electrolytic Capacitors
Electrolytic capacitors are polarized components that offer high capacitance values in a relatively small package. They are widely used in power supply circuits and audio applications due to their ability to store large amounts of energy.
B. Ceramic Capacitors
Ceramic capacitors are non-polarized and are known for their stability and reliability. They are commonly used in high-frequency applications and are available in various capacitance values.
C. Film Capacitors
Film capacitors utilize a thin plastic film as the dielectric material. They are known for their low loss and high stability, making them suitable for applications in audio equipment and power electronics.
D. Tantalum Capacitors
Tantalum capacitors are known for their high capacitance-to-volume ratio and reliability. They are often used in compact electronic devices, such as smartphones and laptops.
E. Other Types
Other types of capacitors include supercapacitors, which offer high energy density and rapid charge/discharge capabilities, and aluminum capacitors, which are commonly used in power supply circuits.
III. Raw Materials
The production of capacitors begins with the selection of high-quality raw materials. The primary materials used in capacitor production include:
A. Overview of Materials Used in Capacitor Production
1. **Dielectric Materials**: The dielectric material is crucial for a capacitor's performance, as it determines the capacitor's capacitance and voltage rating. Common dielectric materials include ceramic, polyester, polypropylene, and tantalum oxide.
2. **Conductive Materials**: Conductive materials, such as aluminum, tantalum, and copper, are used for the electrodes. The choice of conductive material affects the capacitor's efficiency and performance.
3. **Electrolytes**: In electrolytic capacitors, electrolytes play a vital role in enabling the flow of electric current. Liquid or solid electrolytes are used, depending on the capacitor type.
B. Sourcing and Quality Control of Raw Materials
Sourcing high-quality raw materials is essential for ensuring the reliability and performance of capacitors. Manufacturers often establish relationships with trusted suppliers and implement strict quality control measures to verify the purity and consistency of materials.
IV. Production Process
The production process of capacitors involves several key steps, from design and engineering to manufacturing and quality control.
A. Design and Engineering
1. **Specifications and Requirements**: The first step in the production process is defining the specifications and requirements for the capacitor. This includes determining the desired capacitance, voltage rating, and physical dimensions.
2. **Prototyping and Testing**: Once the specifications are established, prototypes are created and tested to ensure they meet performance criteria. This phase is critical for identifying potential issues before mass production.
B. Manufacturing Steps
1. **Dielectric Layer Preparation**:
- **Material Selection**: The choice of dielectric material is crucial for the capacitor's performance. Manufacturers select materials based on the desired electrical properties and application requirements.
- **Layer Thickness and Uniformity**: The dielectric layer must be applied uniformly to ensure consistent performance. Advanced techniques, such as sputtering or chemical vapor deposition, are often used to achieve the desired thickness.
2. **Electrode Fabrication**:
- **Material Deposition Techniques**: Electrodes are fabricated using various deposition techniques, such as physical vapor deposition (PVD) or chemical vapor deposition (CVD). These methods ensure a high-quality conductive layer.
- **Patterning and Etching**: After deposition, the electrodes are patterned and etched to create the desired shapes and sizes. This step is critical for ensuring proper electrical connections.
3. **Assembly of Capacitor Components**:
- **Layer Stacking**: The dielectric layer and electrodes are stacked together to form the capacitor structure. This process requires precision to ensure proper alignment and contact.
- **Connection of Electrodes**: The electrodes are connected to external leads, allowing the capacitor to be integrated into electronic circuits.
4. **Encapsulation and Packaging**:
- **Protective Coatings**: Capacitors are often coated with protective materials to enhance durability and prevent environmental damage. This step is particularly important for electrolytic capacitors.
- **Final Assembly**: The final assembly involves packaging the capacitors in suitable enclosures, ensuring they are ready for shipment and use in electronic devices.
C. Quality Control
Quality control is a critical aspect of capacitor production, ensuring that each component meets industry standards and performance requirements.
1. **Testing for Electrical Performance**: Capacitors undergo rigorous testing to verify their electrical performance, including capacitance, voltage rating, and leakage current.
2. **Reliability Testing**: Reliability tests, such as temperature cycling and humidity exposure, are conducted to assess the long-term performance of capacitors under various conditions.
3. **Compliance with Industry Standards**: Manufacturers must ensure that their products comply with industry standards, such as those set by the International Electrotechnical Commission (IEC) and the Institute of Electrical and Electronics Engineers (IEEE).
V. Environmental Considerations
As the electronics industry grows, so does the need for sustainable practices in capacitor production.
A. Sustainable Practices in Capacitor Production
Manufacturers are increasingly adopting sustainable practices, such as reducing waste, optimizing energy consumption, and using eco-friendly materials. These efforts not only benefit the environment but also enhance the company's reputation.
B. Recycling and Disposal of Capacitors
Proper recycling and disposal of capacitors are essential to minimize environmental impact. Many manufacturers are exploring ways to recycle materials from old capacitors, reducing the need for new raw materials.
C. Regulatory Compliance and Environmental Impact
Compliance with environmental regulations is crucial for capacitor manufacturers. This includes adhering to laws regarding hazardous materials and waste management, ensuring that production processes do not harm the environment.
VI. Innovations in Capacitor Technology
The capacitor industry is continually evolving, driven by advancements in materials and technology.
A. Advances in Materials and Design
Innovations in dielectric materials and electrode design are leading to capacitors with improved performance characteristics, such as higher capacitance values and lower equivalent series resistance (ESR).
B. Impact of Technology on Production Efficiency
Automation and advanced manufacturing techniques are enhancing production efficiency, reducing costs, and improving product quality. Technologies such as machine learning and artificial intelligence are being integrated into the production process to optimize operations.
C. Future Trends in Capacitor Manufacturing
The future of capacitor manufacturing is likely to be shaped by trends such as miniaturization, increased energy density, and the development of new materials, such as graphene and nanomaterials. These advancements will enable the production of capacitors that meet the demands of next-generation electronic devices.
VII. Conclusion
In summary, the production process of mainstream capacitors is a complex and multifaceted endeavor that involves careful consideration of materials, design, and manufacturing techniques. Capacitors play a vital role in modern electronics, and as technology continues to advance, the demand for innovative and efficient capacitor solutions will only grow. By embracing sustainable practices and investing in research and development, the capacitor industry can ensure a bright future, contributing to the ongoing evolution of electronic devices and systems.