What Components and Modules Does a Resistor Manufacturer Include?
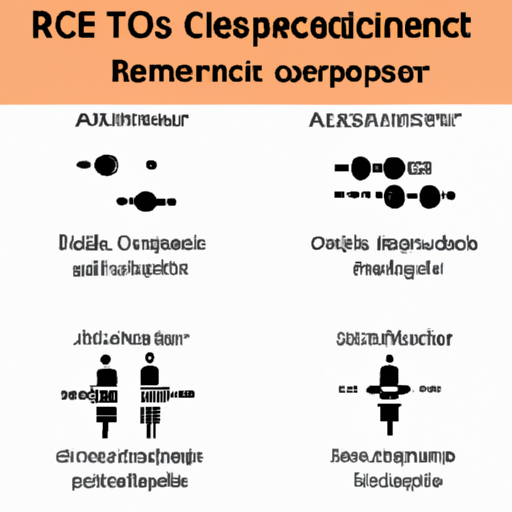
I. Introduction
Resistors are fundamental components in electronic circuits, serving the crucial role of controlling the flow of electric current. By providing resistance, they help to manage voltage levels, protect sensitive components, and ensure the proper functioning of electronic devices. The manufacturing of resistors is a complex process that involves various components and modules, each contributing to the final product's quality and performance. In this blog post, we will explore the different types of resistors, the key components involved in their manufacturing, the modules that make up the production process, and the environmental and safety considerations that manufacturers must adhere to.
II. Types of Resistors
Resistors come in various types, each designed for specific applications and performance characteristics. Understanding these types is essential for grasping the complexity of resistor manufacturing.
A. Fixed Resistors
Fixed resistors are the most common type, providing a constant resistance value. They are widely used in electronic circuits.
1. **Carbon Composition Resistors**: Made from a mixture of carbon particles and a binding resin, these resistors are known for their high energy absorption and ability to withstand high temperatures. However, they have a higher tolerance and lower stability compared to other types.
2. **Metal Film Resistors**: These resistors are made by depositing a thin layer of metal onto a ceramic substrate. They offer better precision and stability than carbon composition resistors, making them suitable for applications requiring high accuracy.
3. **Wirewound Resistors**: Constructed by winding a metal wire around a ceramic or fiberglass core, wirewound resistors can handle high power levels and are often used in power applications. They are known for their durability and reliability.
B. Variable Resistors
Variable resistors allow for adjustable resistance values, making them versatile components in electronic circuits.
1. **Potentiometers**: These are commonly used for volume control in audio equipment and as adjustable voltage dividers. They consist of a resistive element and a movable contact.
2. **Rheostats**: Similar to potentiometers but designed to handle higher currents, rheostats are used in applications where variable resistance is needed, such as in light dimmers.
C. Specialty Resistors
Specialty resistors are designed for specific applications and often have unique properties.
1. **Thermistors**: These temperature-sensitive resistors change resistance with temperature variations. They are widely used in temperature sensing and control applications.
2. **Photoresistors**: Also known as light-dependent resistors (LDRs), these components change resistance based on light exposure. They are commonly used in light-sensing applications, such as automatic lighting systems.
III. Key Components in Resistor Manufacturing
The manufacturing of resistors involves several key components that contribute to the quality and performance of the final product.
A. Raw Materials
1. **Conductive Materials**: The choice of conductive materials is critical in resistor manufacturing. Common materials include carbon, metal oxides, and metal films. Each material has its own properties that affect the resistor's performance, such as temperature coefficient and stability.
2. **Insulating Materials**: Insulating materials, such as ceramics and plastics, are used to encase the resistive element. These materials must withstand high temperatures and provide electrical insulation to prevent short circuits.
B. Manufacturing Equipment
1. **Mixing and Molding Machines**: These machines are used to combine raw materials and shape them into the desired form. The mixing process ensures a uniform distribution of conductive materials, while molding machines create the physical structure of the resistor.
2. **Sintering Furnaces**: Sintering is a process that involves heating the molded resistors to a temperature below their melting point, allowing the particles to bond together. This step is crucial for achieving the desired electrical and mechanical properties.
3. **Laser Trimming Machines**: After the resistors are manufactured, laser trimming machines are used to precisely adjust the resistance value. This process ensures that the resistors meet the specified tolerances and performance standards.
C. Quality Control Instruments
1. **Multimeters**: These instruments are essential for measuring resistance, voltage, and current. They are used throughout the manufacturing process to ensure that the resistors meet the required specifications.
2. **Oscilloscopes**: Oscilloscopes are used to analyze the electrical signals in resistors, helping manufacturers identify any issues with performance or stability.
3. **Environmental Testing Chambers**: These chambers simulate various environmental conditions, such as temperature and humidity, to test the durability and reliability of resistors under different operating conditions.
IV. Manufacturing Modules
The resistor manufacturing process can be broken down into several key modules, each playing a vital role in producing high-quality resistors.
A. Design and Prototyping
1. **CAD Software for Resistor Design**: Computer-aided design (CAD) software is used to create detailed designs of resistors, allowing manufacturers to visualize and optimize their products before production.
2. **Prototyping Techniques**: Prototyping is an essential step in the design process, enabling manufacturers to test and refine their designs before mass production. Techniques such as 3D printing and rapid prototyping are commonly used.
B. Production Line
1. **Automated Assembly Processes**: Many resistor manufacturers utilize automated assembly lines to increase efficiency and reduce labor costs. Automation allows for precise and consistent production, minimizing human error.
2. **Manual Assembly Processes**: While automation plays a significant role, some processes still require manual assembly, particularly for specialty resistors or low-volume production runs. Skilled workers are essential for ensuring quality in these cases.
C. Testing and Quality Assurance
1. **In-line Testing Procedures**: Throughout the production process, in-line testing is conducted to monitor the quality of resistors. This includes measuring resistance values and checking for defects.
2. **Final Inspection Protocols**: Before packaging and shipping, resistors undergo final inspections to ensure they meet all specifications and quality standards. This step is crucial for maintaining customer satisfaction and product reliability.
V. Environmental and Safety Considerations
As with any manufacturing process, environmental and safety considerations are paramount in resistor production.
A. Compliance with Regulations
Manufacturers must comply with various regulations, such as the Restriction of Hazardous Substances (RoHS) and Registration, Evaluation, Authorisation and Restriction of Chemicals (REACH). These regulations aim to minimize the environmental impact of electronic components and ensure the safety of consumers.
B. Waste Management and Recycling
Effective waste management practices are essential in resistor manufacturing. Manufacturers are encouraged to implement recycling programs for raw materials and packaging to reduce their environmental footprint.
C. Safety Measures in Manufacturing
Safety measures, such as proper ventilation, personal protective equipment (PPE), and training programs, are critical in ensuring the safety of workers in resistor manufacturing facilities. Manufacturers must prioritize the health and safety of their employees while maintaining efficient production processes.
VI. Conclusion
In summary, the manufacturing of resistors involves a complex interplay of various components and modules, from raw materials and manufacturing equipment to design and quality assurance processes. Understanding these elements is essential for appreciating the intricacies of resistor production and the importance of innovation in the industry. As technology continues to advance, the future of resistor manufacturing will likely see further improvements in efficiency, sustainability, and performance, ensuring that these vital components continue to play a crucial role in the ever-evolving world of electronics.
What Components and Modules Does a Resistor Manufacturer Include?
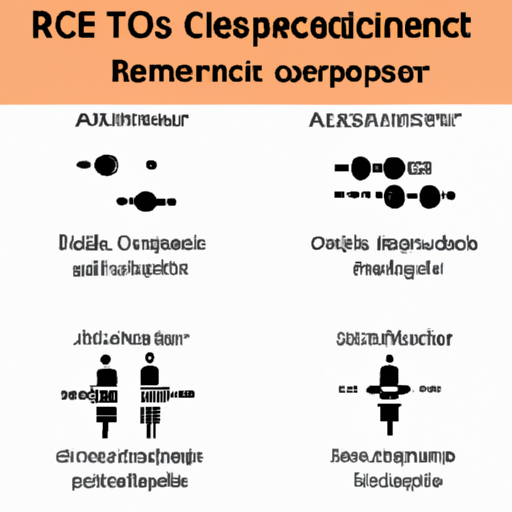
I. Introduction
Resistors are fundamental components in electronic circuits, serving the crucial role of controlling the flow of electric current. By providing resistance, they help to manage voltage levels, protect sensitive components, and ensure the proper functioning of electronic devices. The manufacturing of resistors is a complex process that involves various components and modules, each contributing to the final product's quality and performance. In this blog post, we will explore the different types of resistors, the key components involved in their manufacturing, the modules that make up the production process, and the environmental and safety considerations that manufacturers must adhere to.
II. Types of Resistors
Resistors come in various types, each designed for specific applications and performance characteristics. Understanding these types is essential for grasping the complexity of resistor manufacturing.
A. Fixed Resistors
Fixed resistors are the most common type, providing a constant resistance value. They are widely used in electronic circuits.
1. **Carbon Composition Resistors**: Made from a mixture of carbon particles and a binding resin, these resistors are known for their high energy absorption and ability to withstand high temperatures. However, they have a higher tolerance and lower stability compared to other types.
2. **Metal Film Resistors**: These resistors are made by depositing a thin layer of metal onto a ceramic substrate. They offer better precision and stability than carbon composition resistors, making them suitable for applications requiring high accuracy.
3. **Wirewound Resistors**: Constructed by winding a metal wire around a ceramic or fiberglass core, wirewound resistors can handle high power levels and are often used in power applications. They are known for their durability and reliability.
B. Variable Resistors
Variable resistors allow for adjustable resistance values, making them versatile components in electronic circuits.
1. **Potentiometers**: These are commonly used for volume control in audio equipment and as adjustable voltage dividers. They consist of a resistive element and a movable contact.
2. **Rheostats**: Similar to potentiometers but designed to handle higher currents, rheostats are used in applications where variable resistance is needed, such as in light dimmers.
C. Specialty Resistors
Specialty resistors are designed for specific applications and often have unique properties.
1. **Thermistors**: These temperature-sensitive resistors change resistance with temperature variations. They are widely used in temperature sensing and control applications.
2. **Photoresistors**: Also known as light-dependent resistors (LDRs), these components change resistance based on light exposure. They are commonly used in light-sensing applications, such as automatic lighting systems.
III. Key Components in Resistor Manufacturing
The manufacturing of resistors involves several key components that contribute to the quality and performance of the final product.
A. Raw Materials
1. **Conductive Materials**: The choice of conductive materials is critical in resistor manufacturing. Common materials include carbon, metal oxides, and metal films. Each material has its own properties that affect the resistor's performance, such as temperature coefficient and stability.
2. **Insulating Materials**: Insulating materials, such as ceramics and plastics, are used to encase the resistive element. These materials must withstand high temperatures and provide electrical insulation to prevent short circuits.
B. Manufacturing Equipment
1. **Mixing and Molding Machines**: These machines are used to combine raw materials and shape them into the desired form. The mixing process ensures a uniform distribution of conductive materials, while molding machines create the physical structure of the resistor.
2. **Sintering Furnaces**: Sintering is a process that involves heating the molded resistors to a temperature below their melting point, allowing the particles to bond together. This step is crucial for achieving the desired electrical and mechanical properties.
3. **Laser Trimming Machines**: After the resistors are manufactured, laser trimming machines are used to precisely adjust the resistance value. This process ensures that the resistors meet the specified tolerances and performance standards.
C. Quality Control Instruments
1. **Multimeters**: These instruments are essential for measuring resistance, voltage, and current. They are used throughout the manufacturing process to ensure that the resistors meet the required specifications.
2. **Oscilloscopes**: Oscilloscopes are used to analyze the electrical signals in resistors, helping manufacturers identify any issues with performance or stability.
3. **Environmental Testing Chambers**: These chambers simulate various environmental conditions, such as temperature and humidity, to test the durability and reliability of resistors under different operating conditions.
IV. Manufacturing Modules
The resistor manufacturing process can be broken down into several key modules, each playing a vital role in producing high-quality resistors.
A. Design and Prototyping
1. **CAD Software for Resistor Design**: Computer-aided design (CAD) software is used to create detailed designs of resistors, allowing manufacturers to visualize and optimize their products before production.
2. **Prototyping Techniques**: Prototyping is an essential step in the design process, enabling manufacturers to test and refine their designs before mass production. Techniques such as 3D printing and rapid prototyping are commonly used.
B. Production Line
1. **Automated Assembly Processes**: Many resistor manufacturers utilize automated assembly lines to increase efficiency and reduce labor costs. Automation allows for precise and consistent production, minimizing human error.
2. **Manual Assembly Processes**: While automation plays a significant role, some processes still require manual assembly, particularly for specialty resistors or low-volume production runs. Skilled workers are essential for ensuring quality in these cases.
C. Testing and Quality Assurance
1. **In-line Testing Procedures**: Throughout the production process, in-line testing is conducted to monitor the quality of resistors. This includes measuring resistance values and checking for defects.
2. **Final Inspection Protocols**: Before packaging and shipping, resistors undergo final inspections to ensure they meet all specifications and quality standards. This step is crucial for maintaining customer satisfaction and product reliability.
V. Environmental and Safety Considerations
As with any manufacturing process, environmental and safety considerations are paramount in resistor production.
A. Compliance with Regulations
Manufacturers must comply with various regulations, such as the Restriction of Hazardous Substances (RoHS) and Registration, Evaluation, Authorisation and Restriction of Chemicals (REACH). These regulations aim to minimize the environmental impact of electronic components and ensure the safety of consumers.
B. Waste Management and Recycling
Effective waste management practices are essential in resistor manufacturing. Manufacturers are encouraged to implement recycling programs for raw materials and packaging to reduce their environmental footprint.
C. Safety Measures in Manufacturing
Safety measures, such as proper ventilation, personal protective equipment (PPE), and training programs, are critical in ensuring the safety of workers in resistor manufacturing facilities. Manufacturers must prioritize the health and safety of their employees while maintaining efficient production processes.
VI. Conclusion
In summary, the manufacturing of resistors involves a complex interplay of various components and modules, from raw materials and manufacturing equipment to design and quality assurance processes. Understanding these elements is essential for appreciating the intricacies of resistor production and the importance of innovation in the industry. As technology continues to advance, the future of resistor manufacturing will likely see further improvements in efficiency, sustainability, and performance, ensuring that these vital components continue to play a crucial role in the ever-evolving world of electronics.